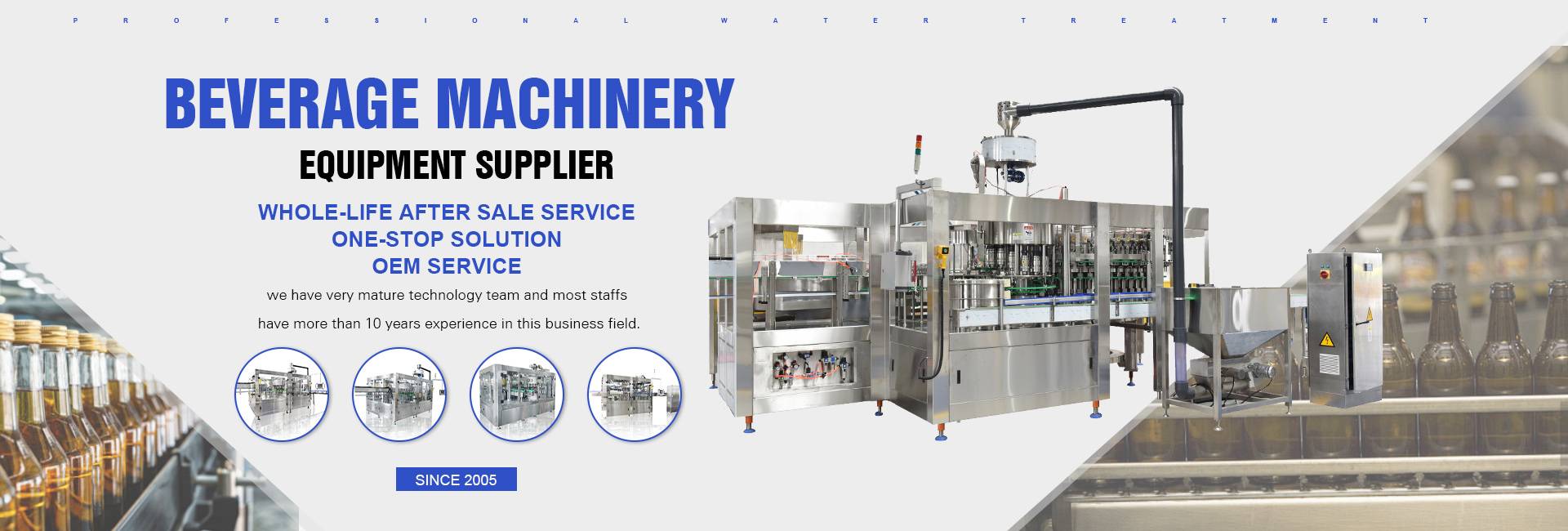
Higee Automatic Red Wine Glass Bottle Liquid Filling Machines Beverage And Wine Bottling Liquid Production Line
Model: BDGF14-12-5
Speed: 2500BPH
Bottle size: 500ML
Working position: 14 rinsing, 12 filling, 5 capping
Filling accuracy: 0~1ml
Filling temperature: 0~5°C
Main Material: SUS304 or SS316L
Power: 2.02kw
Water consumption: 1.5t/h
Pressure of air source: 0.06~0.2MPa
Dimension: 2400×1770×2700 (L*W*H)
Weight: 2000kg
Usage: carbonated soft drink, sparkling wine,carbonated juice, sparkling water.
Certification: CE, ISO
- Small Bottle 0.2L~2L Filler
- Beer&Wine Filler
- Aluminum & Tin Can Filler
- Plastic Bottle 3L~7L Filler
- Plastic Barrel 10L~25L Filler
- PET Bottle Blow Molding Machine
- Water Treatment System
- OPP Hot Melt Labeling Machine
- Adhesive Sticker Labeling Machine
- Film Wrapping Packing Machine
- PVC SLeeve Shrink Labeling Machine
- Beverage Juice Mixing Process System
- Carton Packing Machine
- Small Bottle 0.2L~2L Filler
- Beer&Wine Filler
- Aluminum & Tin Can Filler
- Plastic Bottle 3L~7L Filler
- Plastic Barrel 10L~25L Filler
- PET Bottle Blow Molding Machine
- Water Treatment System
- OPP Hot Melt Labeling Machine
- Adhesive Sticker Labeling Machine
- Film Wrapping Packing Machine
- PVC SLeeve Shrink Labeling Machine
- Beverage Juice Mixing Process System
- Carton Packing Machine

With such a wide range of technical solutions, Fillers Machinery company is able to offer a manufacturing scenario that best fits its customer’s requirements, taking into account factors such as bottle cost, energy savings, space, and the need for flexibility.
This BDGF Wash-filling-capping 3-in-1unit:introduced by foreign advanced gas-filling technique is a high performance fully automatic liquid packaging equipment.
Machine for carbonated beverage packaging machine has the following characteristics: filling tank, filling valves and other components in direct contact with the material are high-quality stainless steel or non-toxic materials, in line with food hygiene requirements: use of resistant seals hot rubber to meet the high-temperature sterilization process of user requirements: PLC programmable controller used to realize from the bottle into the machine to the packaging of finished using the automatic control of frequency control, easy to transfer the user to adjust prepared to meet the different process on the capacity requirements; using isobaric filling principle and popular spring-loaded valves, ensuring the quality of the beverage, using an advanced magnetic clutch adjustment screw cap torque device to ensure the quality of the blocks.
1. This machine adopts a fully automatic working method, which automatically completes the station transfer of the bottle and the cleaning and filling of each station, without manual operation by personnel.
2. Equipped with a separate cleaning function, it only cleans without filling, and can be used as a pre-washing machine.
3. The mechanical transmission mechanism adopts the linkage of mechanical curved rods, so that the beer filling machine runs smoothly, reliably, and accurately positioned, and avoids the occurrence of failure rates.
4. The equipment is equipped with automatic flow detection, pressure detection, residual liquid detection after purging, wine spear opening detection and other detection functions, and has a station alarm.
5. Filling adopts CO2 back-up pressure and pressure-holding low-pressure fully-closed filling method. The filling volume is detected by imported flowmeter, which can ensure low foam, low consumption and accurate filling volume of the wine after filling.
6. The water tank automatically replenishes water, automatically heats and maintains a constant temperature.
7. The equipment can set and adjust the filling capacity through the touch screen, and can adjust the error, and can display the number of filled bottles and liters in real time.
Rinsing Unit
– Into bottle way is air conveyor direct connection with bottle dial.
– All 304/316 stainless steel rinse heads, water spray style inject design, more save water consumption and more clean.
– 304/316 Stainless steel Gripper with plastic pad, ensure minimal bottle crash during washing.
– 304/316 stainless steel washing pump make the machine more durable.
The sliding bearing is from Germany igus company,
wearable & no need lubricate. Nylon catcher is strong and endurable.
Filling Unit
– 304/316 Stainless steel high precision filling nozzle
– Filling volume adjustable in fine rank, same liquid level after filling
– All 304/316 stainless steel contact parts & liquid tank, fine polish, no death corner, easy to clean
– 304/316 stainless steel filling pump
– Efficient spray nozzle rinse thoroughly and save water for flushing
High speed and precision filling technology, filling flow rate is 35% higher than filling technology (reaches to 200ml/s), liquid level precision ≤±2mm;
Capping Unit
– Place and capping system, electromagnetic capping heads, with burden discharge function, make sure minimum bottle crash during capping
– All 304/316 stainless steel construction
– No bottle no capping
– Automatic stop when lack of bottle
– Torque scale is easy for adjustment.
Cooperated Brand
Technical Parameter
Model Rinser-Filler-Capper | BDGF14-12-5 | BDGF16-16-5 | BDGF24-24-8 | BDGF32-32-10 | BDGF40-40-12 | ||
---|---|---|---|---|---|---|---|
Capacity(BPH) | 2500 | 3000 | 5000 | 8000 | 10000 | ||
Suitable to Bottle Shape | Φ=50-120 H=160-320 | ||||||
Power Supply(KW) | 2.02 | 2.42 | 3.12 | 3.92 | 3.92 | ||
Overall dimension(L*W*H)mm | 2400x1770x2700 | 2800x2060x2700 | 2950x2230x2700 | 3700x2650x2700 | 4850x3320x2700 |
Flat Conveyor
- Energy saving. High efficient. Adapt to customer factory layout
- Special lubrication system, keep products clean, health, safety
- Extended service life
- Electric eyes design keep whole line running safety and quickly
- Overload protection mechanism to effectively ensure the safety of the machine
Bottle Labeling and packing
As customer request and market demand, we provide the better solution for the final product package,We have various kinds of options. Labeling machine have the PVC sleeve label, BOPP hot glue label, Adhesive stick label, Wet glue label ,and packing machine have the film shrink machine and carton box package.
Turnkey solution provider
FLSM machinery is committed to being a reliable liquid packaging machinery supplier. Our services range from planning process flow to project coordination and determining the connection of different equipment, so as to provide customers with high-quality, fast and customized services.
Why choose us?
- Turnkey Solution Service
- Installation / Debugging / Training
- After-Sales Service
- Spare Parts
With high-quality equipment, perfect service, abundant operation of the whole plant, and strong turnkey service capability of the whole plant, FLSM helps customers achieve a high-efficiency operation of equipment
After the customers received the equipment, FLSM will send experienced engineers to the customer’s factory to do installation and commission services, and provide theoretical and technical training.
FLSM meets customer requirement in the shortest time with a complete service platform and fast response mechanism.Provide 7*24 hours after-sales service, comprehensive after-sales protection, timely and effective problem solving mechanism.
Providing one-stop spare parts management service solutions, including unified order acceptance, reliable spare parts supply, first-class logistics network, professional service delivery management, to ensure the spare parts are sent to the right place at the right time.
● If we can full fill your request and you are interested in our products, you may pay a visit to the FLSM Company site
● The meaning of visiting a supplier is because seeing is believing; FLSM Company, with its manufacturing and developed& research team, can send you engineers and ensure you after-sales service.
● By letter of credit, you can lock the delivery time easily.
● After the factory visit, You can ensure the facticity of our bank account.
SEE FLSM Company HOW TO ENSURE THE QUALITY!
● To ensure the accuracy of each part, we are equipped with various professional processing equipment and have accumulated professional processing methods over the past years.
● Each component before assembly needs strict control by inspecting personnel.
● Each assembly is in charge by a master who has working experience for more than five years
●After all the equipment is completed, we will connect all the machines and run the full production line for at least 12 hours to ensure stable running in the customers’ factory
THE AFTER-SALE SERVICE OF FLSM Company!
● After finishing the production, we will debug the production line, take photos, videos and send them to customers via mail or
instant tools
● After the commissioning, we will package the equipment by standard export package for shipment.
● According to the customer’s request, we can arrange for our engineers to come to the customer’s factor customers factory for training.
● Engineers, sales managers, and after-sales service managers will form an after-sales team, online and offline, to follow the customers’ project.